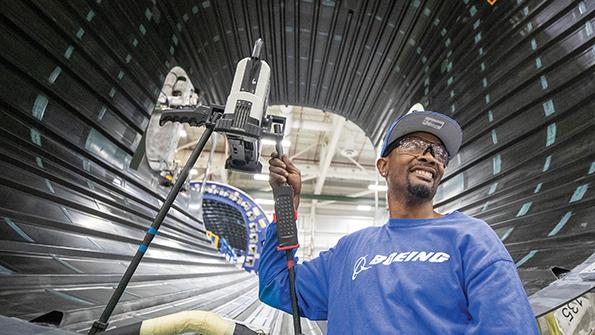
New surface verification tools, such as 8tree’s Dentcheck, help ensure quality on key structural joins, including at Section 48 (pictured).
Years of undetected production mistakes mean most of the 1,120 Boeing 787s in service do not meet the manufacturer’s own standards, which the FAA approved and considers nonnegotiable. While the mistakes must be fixed on any newly built aircraft, Boeing has no risk concerns for its in-service fleet, and its analysis shows little if any additional work will be needed to ensure that 787s remain safe.
The 787 fleet safety outreach, which included half a day of media briefings at Boeing’s 787 final assembly facility in North Charleston, South Carolina, was prompted by an employee’s claims questioning the company’s processes and willingness to address serious concerns. The manufacturer pushed back firmly, saying its production processes have improved, the in-service fleet is not at risk, and its employees are heard.
- The OEM defends 787 fleet safety and production process
- Extensive testing and fleet performance underpin its safety record
- Conservative tolerances and composite design prove beneficial
Most 787s delivered before 2020 did not meet Boeing’s design specifications. The OEM says it has fixed the issues in production, and the FAA in mid-2022 signed off on the company’s plan (AW&ST Aug. 29-Sept. 11, 2022, p. 29).
At the heart of the controversy are concerns that the nonconforming gaps between the 787’s all-composite, one-piece fuselage barrel sections pose long-term safety risks to affected airframes. Boeing Quality Engineer Sam Salehpour says the company is not addressing the gap issues and is knowingly violating standards, such as how much force can be used in the fit-up process that aligns fuselage sections and other parts before they are attached.
Lawyers representing Salehpour, who went public via an April 9 article in The New York Times, sent a whistleblower letter to the FAA in January outlining his concerns. He cited internal Boeing documents—including a white paper from engineers with similar critiques—to support his claims, adding that the company ignored his appeals and transferred him out of the 787 program. Aviation Week requested copies of the documents, but the law firm did not provide them.
Gaps, common in any airframe assembly, stem from various issues. On the 787, their most prevalent cause is mismatched inner-skin surfaces of connected fuselage sections. If one section is not as smooth as the adjacent one, gaps will be left under the band, or splice plate, that overlaps the join between the two circular barrel sections. In some areas, Boeing sands fuselage edges by hand to ensure they meet surface smoothness requirements.
Gaps detected during assembly that are deemed too large to be closed are filled with small pieces of material called shims. If the shims are not the correct size, however, the structure may not conform to specifications.
All of these issues left nonconforming gaps on the first 980 787s built. Boeing did not discover most of them until 2019-20, when a supplier flagged issues with its parts and prompted Boeing—at the FAA’s insistence—to pause deliveries in late 2020 and launch a full-scale production review.
Newly built aircraft that do not conform to design specifications cannot be delivered, so Boeing halted deliveries to assess the problem’s scope and to develop an FAA-approved gap management plan to inspect completed airframes. By the time the FAA signed off on the plan in July 2022, the manufacturer—which kept 787 production flowing at a reduced rate to avoid a full factory shutdown—had 120 undelivered aircraft in its inventory. Each required rework; there are still about 40 left in the queue.
A production nonconformance is not the same as an immediate or long-term safety-of-flight issue. Boeing quickly determined none of the production mistakes presented an immediate risk to the in-service fleet. But it still had to assess potential ramifications over 20-30 years of flying as part of its routine continued operational safety process.
The biggest concern: whether any of the nonconforming work affects the transfer of loads across the joins and, potentially, the structural margin.
Load transfer considerations between fuselage sections are important because composite structures are very stiff, unlike conventional aluminum airframes, which are flexible. Any issues that could interfere with the load transfer between sections—such as gaps, improperly installed shims or inner-skin surfaces that are not smooth—can form a focus for stress buildup.
Design loads on the airframe structure include forces and moments generated by aerodynamic pressure, maneuvers and gusts, as well as other loads, such as cabin pressurization, inertia and landing impact. The loads must be distributed through pathways to ensure the aircraft structure can withstand the design loads without exceeding the allowable limits on deflection, displacement, stress or strains. Tight connections between fuselage pieces and other load-bearing parts are critical.

In the 787, the joins between the composite fuselage sections must be able to transfer a wide range of shear, tensile and static loads safely while maintaining damage tolerance. Shear and fatigue loads are carried mainly across the joins from Section 44 aft through Sections 46, 47 and 48, while tensile and fatigue loads are carried predominantly via the crown of Sections 41/43 aft through Section 47.
Static ground loads from the nose and main landing gear legs are transferred through Section 41 and through Sections 11/43 and 45/46, respectively. Load transfer for damage tolerance is required particularly in the forward fuselage from Section 41 aft through Section 44 as well as in the aft fuselage from Section 46 through Section 48.
The focus for several key gap conformance issues originated not only in the joins between major subsections on the 787 final assembly line but also between subassembly sections provided by supplier partners. These notably included the forward fuselage Sections 41 and 43—made by Spirit AeroSystems and Kawasaki Heavy Industries (KHI)—and the interfaces between the midbody Sections 44 and 46 made by Leonardo. Further issues also cropped up in the interfaces between the Leonardo subassembly and the Boeing-built Section 47.
Another area that accounted for several nonconforming gaps and profile issues is the complicated aft section, comprised of Boeing’s Section 47 and 48 and the Korean Air-built Section 48 Aft tail cone. Gaps around the splice line between the two Boeing-made units at the aft pressure bulkhead exceeded Boeing’s 0.005-in. inner mold line flatness over a 5-in.-span criteria in multiple instances. Validating 47/48 join gap sizes on the remaining inventoried aircraft requires removing every fastener—more than 2,000—and conducting through-hole checks using angled feeler gauges.
Salehpour alleges that excessive fit-up force used while joining composite fuselage sections compromised affected airframes. Pressure is required to bring parts together because of the relative stiffness of composites compared with aluminum, but the amount of pressure is limited to ensure the process remains within design tolerances. The limit is designed to prevent microcracking of the resin within the composite material, which could lead to disbonding of the fibers over time.
During Boeing’s audits of internally and externally provided subassemblies, the company discovered several instances where design changes or new procedures were needed to correct nonconformances. One example: Clamping forces Leonardo used during pre-fit assembly on parts of Section 44/46 were up to 50 lb. per linear foot compared with Boeing’s maximum requirement of 10 lb., according to documents seen by Aviation Week (AW&ST Dec. 12-25, 2022, p. 28).
In other cases, such as the Boeing-built horizontal stabilizer, the company acknowledged that the clamping forces used were incorrect—and in some instances unknown—compared with the 5-lb.-per-foot allowed force. For some assemblies, such as the KHI-supplied Section 43, investigations showed that even when the requisite 5-lb. fit-up force was used, the gap exceeded Boeing’s maximum allowable 0.008 in.
Boeing’s in-service fleet risk analysis leans on routine maintenance inspection data and extensive full-scale fatigue and static tests. Its conclusion: The 787 is safe from concerns over potential progressive fatigue in the aircraft’s primary composite structure, Steve Chisholm, vice president and chief engineer for mechanical and structural engineering, said during a media briefing. In-depth checks on aircraft ranging from six-year inspections to 12-year heavy maintenance teardowns have shown “zero airframe fatigue findings on the 787 fleet,” he noted.

“We have over 600 airplanes that have completed a heavy maintenance check, which is [at least] six years of operation, where they’re opening up the structures, pulling back the insulation blankets, taking off the sidewalls and looking at things,” he continued. “We have another eight airplanes that have actually gotten to the 12-year heavy maintenance check.”
Boeing has augmented scheduled maintenance checks with additional inspections from its specialists under a structural maintenance economic evaluation program involving 10 airframes. “We also sent teams of our engineers out—structures engineers, nondestructive inspection specialists, and finishes and corrosion specialists to collect data during heavy maintenance checks,” Chisholm said. He added that the data, culled from the heavy checks and 671 aircraft undergoing the less invasive six-year inspection, has “been shared with the FAA.”
In-service reviews of the oldest and most used airframes underpin results from tests done early in the program to validate the 787’s design—tests that unknowingly trialed production flaws discovered years later.
“The most impactful data is the data that we got from our full-scale fatigue test,” Chisholm said. “The build condition [was] the same as what we saw in the later build.”
Put another way, the same nonconformances that crept into the first 980 aircraft were present in the fatigue test article.
While the revelation does not reflect well on Boeing’s original quality assurance process, it bolsters the argument that its design—including material selection and tolerances—is robust.
“In over 165,000 cycles, there were zero fatigue issues in the composite structure,” Chisholm said.
The tests, which began in September 2010 on ZY998, the third 787 airframe built, ran through 2015 and simulated entire flights, from taxi through ascent, cruise, descent and back to taxi (AW&ST Dec. 21, 2015-Jan. 3, 2016, p. 51). Targeted at creating a dataset for the airframe’s durability, the tests subjected the structure to loads that simulated more than 3.6 times the design life of 44,000 flight cycles.
Testing was conducted in a steel rig weighing more than 1 million lb. at the Boeing manufacturing plant in Everett, Washington. The rig included more than 100 mechanical connections to push, pull and twist the 182-ft.-long fuselage, wing forward leading edge and vertical stabilizer. The 787 structure incorporated over 3,000 sensors that evaluated more than 40 million discrete load conditions as the airframe was subjected to shear forces, bending moments and torsion loads typically experienced during five flight conditions ranging from benign to extremely turbulent.
Although some parts failed over the course of testing, they were all metallic. Components and parts that cracked or failed prematurely included a metal bearing pad in the main landing-gear support structure and tie-rod end lug and support fittings. There were no catastrophic failures during the test, Boeing adds.
The fatigue-test airframe incorporated additional sensors along the side-of-body wingbox joint, which was reinforced after earlier static tests revealed weakness in the area. The redesign, which pushed back first flight of the 787 to December 2009, was validated in static tests the previous month and later incorporated into ZY998. Compared with fatigue tests on earlier metallic airframes, the 787 test unit included more sensors on various stiffener terminations and more extensive periodic inspections than required by the baseline maintenance program.
Average 787 utilization is about 600 cycles per year, Boeing said. The busiest aircraft operate 900-1,400 cycles annually, Aviation Week Network Fleet Discovery data show. The highest-time 787, an All Nippon Airways 787-8, has flown 16,500 cycles in its 11-year service life.
The 44,000-cycle life expectancy is reflected in the extent of the 787 tests compared with previous fatigue tests on conventional aluminum-built airframes, such as the 777, which completed the then-record number of 120,000 simulated cycles in 1997. This represented the equivalent of 60 years in operation or twice the 777’s design service objective (DSO) of 60,000 flights. The DSOs of the 787 and 777 have both been significantly extended beyond previous generations, such as the 757 and 767, which underwent fatigue tests simulating 100,000 flights, or twice a 20-year DSO of 50,000 flights.
Results from the tests, in-service fleet maintenance checks and other Boeing analysis give the company confidence that operational 787s with production flaws are not at risk and will not require invasive rework.
“We have not closed all of those items,” Chisholm said. “We’re still in that discussion with the FAA, and we expect to be done by the end of the year. But we have not seen anything in service related to gap management that would indicate that there is an issue with the in-service fleet.”
Salehpour’s claims of internal deaf ears and retaliation track with what an independent panel found during its recently completed six-month investigation ordered by U.S. lawmakers (AW&ST March 25-April 7, p. 14). Boeing insists efforts to redouble its employee “speak-up” policy are paying off.
“We know we have more work to do, and we are taking action across our company,” Boeing said in a statement, noting a sharp increase in voluntary safety reports since the Jan. 5 Alaska Airlines 1282 door plug blowout accident. That, the company added, “signals progress toward a robust reporting culture that is not fearful of retaliation.”
Comments
787 was a major mistake. Weight savings and fuel savings were virtually zero. Manufacturing costs are massive. Most economic experts who have followed the 787 program say it will never be profitable. The losses at this point are somewhere between $100 - 150 billion. Basic problem is composite frames and stiffeners can't be machined to the tolerances that metal frames and stiffeners can be and so excessive gaps occur. Shims simply can't cure all gapping problems. You can't have knife edge shims.
Problems with the 787 program will dwarf all 737 problems.